From Gaskets to Grommets, Injection Molding Ensures Superior Precision, Durability, & More.
From our homes and hospitals to the roads and factory floors, we rely on a lot of different equipment, machinery, and appliances to power our everyday lives. We want and expect them to work effectively and for a long time before needing repaired or replaced, as all things eventually do. But for this to happen, they must be built well with high-quality, dependable parts and processes.
Essential mechanical components, like grommets, gaskets, bushings, and bearings, are responsible for key functions, including helping seal joints, protecting sensitive areas, and facilitating smooth operation. Without them, our machines and equipment would perform poorly, if at all. The best way to create these components is the process of injection molding.
While there are other molding options for producing these types of parts, including compression molding and transfer molding, injection molding is by far the most effective and preferred one because of the many advantages it offers, including greater precision, cost-effectiveness, and customization. This is why it is so widely used across major industries, such as automotive, electronics, consumer goods, and medical devices.
Utilizing highly advanced injection molding machines, the process involves taking pellets of typically thermoplastic polymers, melting them, and forcing the resulting molten liquid under high pressure into a mold cavity, where it cools and hardens into the desired shape. Once solidified, the mold opens, and the finished part is ejected. The cycle repeats — sometimes in mere seconds — making it ideal for mass production.
Benefits of Injection Molding for Mechanical Parts
-
-
- Greater precision
- Exceptional sealing performance
- Enhanced part strength & durability
- Highly repeatable & uniform
- Able to handle intricate designs
- Cost-effective production
- Superior cycle times
- Noise & vibration dampening
- Environmental resistance
- Seamless integration of features
- Endless customization options
- Minimal waste
- Perfect for small products with high tolerances
- Great for low-finishing requirements in high volumes
-
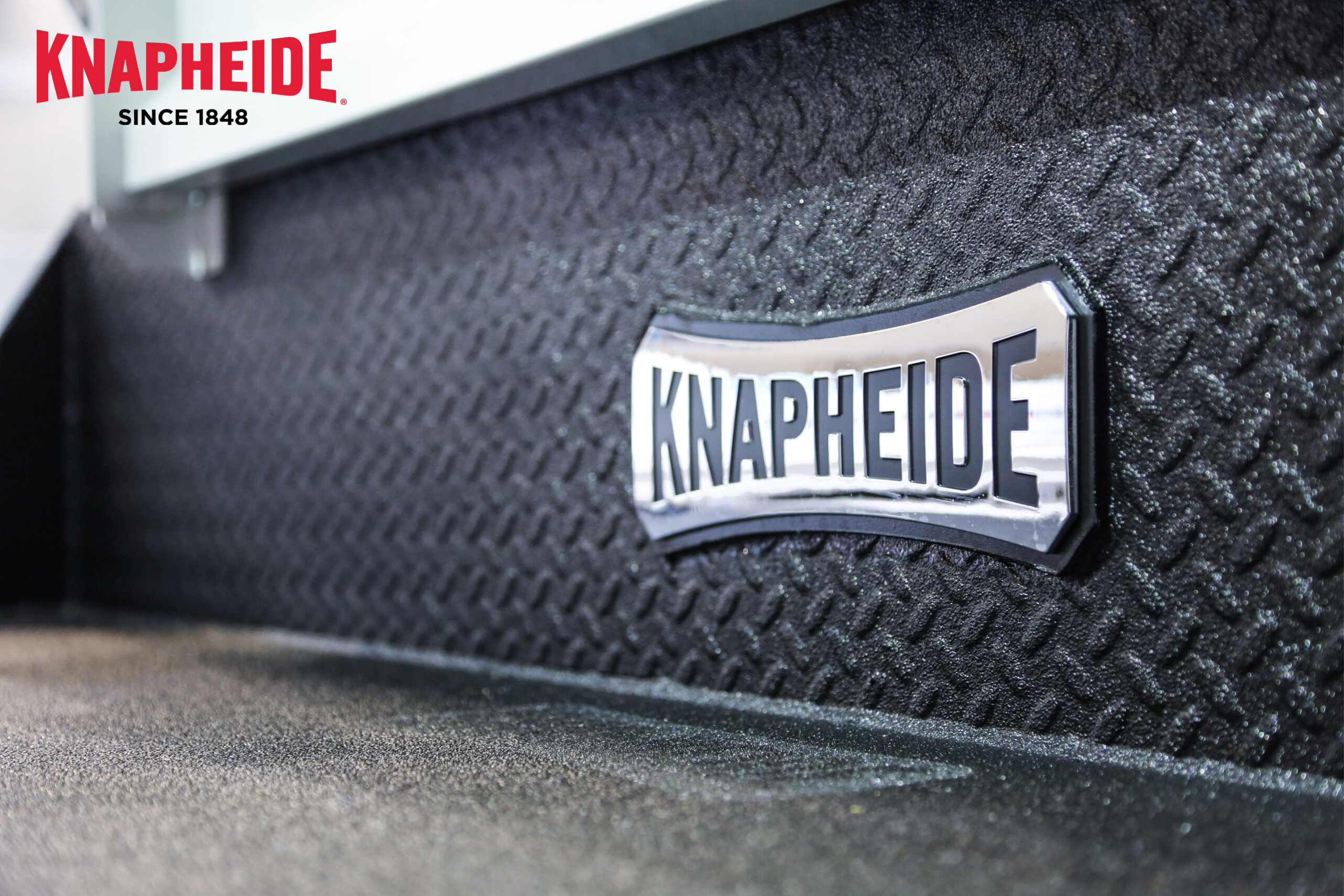
At Form Manufacturing, we have over 20 years of injection molding experience and a proven record of satisfaction with countless clients, making us a trusted partner for those looking to manufacture essential mechanical parts. We have comprehensive molding capabilities and industry-leading equipment to provide you with the high-quality products and seamless customer experience you deserve. Talk to us today about how we can serve your component needs.
While standard parts come in a variety of materials and sizes, off-the-shelf solutions don’t always fully meet an application’s needs. Our custom injection molded mechanical parts will be tailored to your unique application’s requirements, ensuring they offer the exact characteristics you desire.
Custom Components That Form Manufacturing Specializes In
Gaskets
An overarching term for a variety of mechanical seals, gaskets fill the space between two mating components or flanges with flat surfaces to prevent leakage of gases or liquid from or into the joined objects while under compression.
O-Rings
O-rings are circular, ring-shaped gaskets used to stop the leakage of fluids or gases between two mating surfaces when compressed in a groove.
Grommets
Offering cushioning, sealing, and vibration-dampening properties, grommets are small, typically rubber or plastic, components used to reinforce and protect wires, cables, cords, or other items passing through holes in machines and devices.
Bearings
Used in a variety of machines and vehicles, including cars, airplanes, and household appliances, bearings are essential mechanical components that allow for smooth rotation and movement, often to prevent direct metal-to-metal contact between two elements that are in relative motion.
Bushings
Typically used in machinery with rotating or sliding shafts, bushings are essentially sleeves or tubes designed to reduce friction between two moving parts by allowing them to slide against each other with minimal wear. They are also known as sleeve bearings.
To see samples of the high-quality components that Form Manufacturing has produced for others, view our parts gallery.
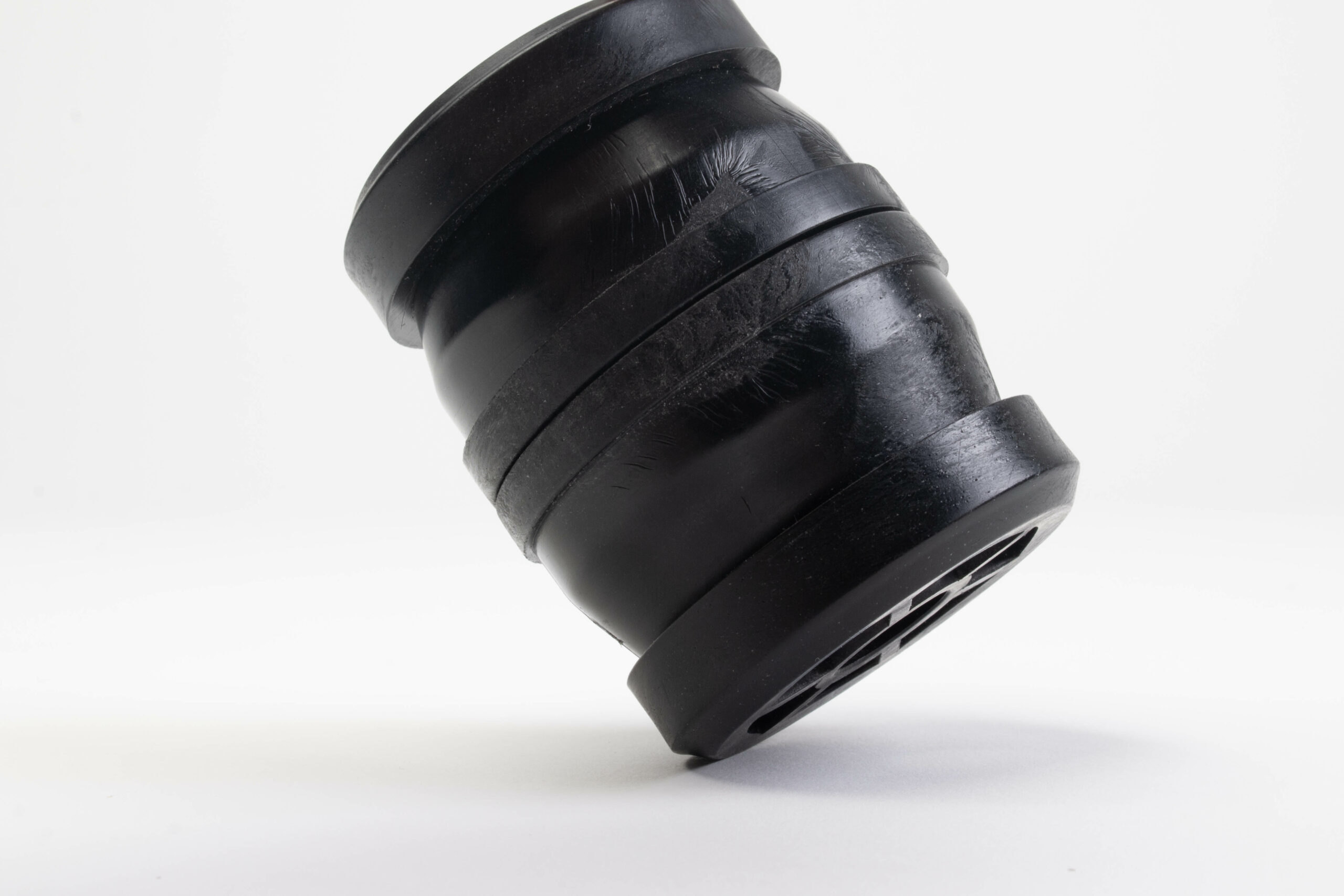
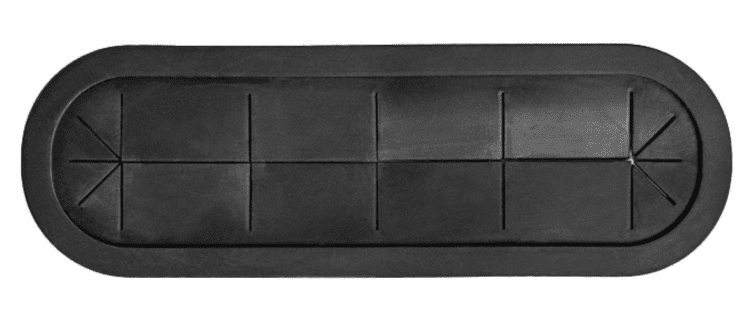
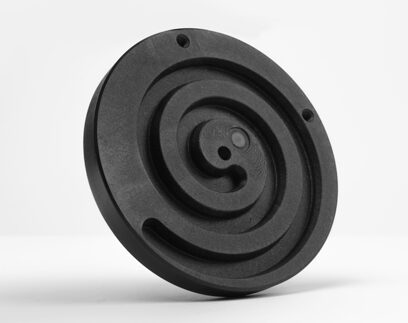
Injection Molding Materials
One of the biggest advantages of injection molding is the ability to tailor material properties for specific applications and requirements. Able to utilize a wide range of plastic materials, each with unique attributes like heat resistance, chemical resistance, or electrical insulation, this customization allows for the selection of materials that best match the demands of the intended application, ultimately optimizing performance and durability. At Form Manufacturing, we offer several material options to choose from, including:
Rigid Plastics
-
-
- LDPE (Low Density Polyethene)
- HDPE (High Density Polyethene)
- Polypropylene (PP)
- PC/ABS (Polycarbonate & ABS Blend)
- Nylon (PA6 & PA66)
- Polycarbonate (PC)
- Acetal (Delrin)
- ASA
- ABS
-
Flexible Plastics
-
-
- TPE (Thermoplastic Elastomer)
- TPU (Thermoplastic Polyurethane)
- TPV (Thermoplastic Vulcanizate)
- EPDM (Type of Rubber)
-
Go here for more details about the injection molding materials Form Manufacturing uses.
Injection molding is the go-to molding process for the manufacturing of essential mechanical components, such as gaskets, grommets, and more. As experts in injection molding, Form Manufacturing is the partner you can trust to craft the high-quality, precise parts you need to ensure reliability and optimal performance. Contact us today with your questions or to request a quote.